As an important thermal processing method, screw extrusion is widely used in feed maturing and sterilizing process. With the popularization of puffing technology in the feed industry, more and more manufacturers are pouring into the puffing equipment manufacturing field. Because there are no relevant national standards in the expansion machine at present, many companies are blindly imitation, non-standard production, and the product quality is low. On the one hand, there are numerous extruder products in the market, and their quality is uneven. On the other hand, users lack relevant expertise and are difficult to identify. They do not know how to choose a suitable expansion device for themselves. As a professional manufacturer of extruders, we are happy to provide advice to our customers on the expansion and related issues that everyone cares about. This article will provide some references on how to choose a suitable extruder.
At present, the screw extrusion extruder in the market can be roughly divided as follows.
From the structure: According to the working part for an axis or two axes is divided into single-screw extruder and twin-screw extruder; single-screw is divided into left-handed right-handed, twin-screw also has the same flat double and opposite flat double points. The single-screw L-screw or right-screw single screw has basically the same change in the properties of the material in the barrel, while the shear strength and the cleaning ability of the material in the same direction and double or opposite direction are significantly different. The most common are the right-handed single screw and the co-rotating twin-screw.
From the working mode: according to whether the material enters the extruder barrel (puffing chamber), whether it is classified into a dry extruder and a wet extruder by steam conditioning. If steam is used for tempering, it is wet working mode; otherwise, it is dry process.
The purpose of steam tempering: to raise the temperature of the material, soften and partially pre-cure the material, add a certain amount of moisture. For most materials, wet puffing is more efficient than dry puffing. Simple analysis is performed considering only the temperature factor. If the expected maturation temperature of the material is 130°C, the dry puffing screw extrusion increases from room temperature (20°C). To this value, the temperature needs to be raised to 110°C. If the wet process is used, the temperature after quenching and tempering is 80°C, and the temperature of the screw extrusion part needs to be raised to 50°C. Therefore, the required mechanical energy is lower than the dry method and more energy is required. Can be used to increase production. In addition, due to the softening of the material, wear on the screw and barrel can also be reduced.
Many users, including some equipment manufacturers, understand literally that water is the wet method. Through the above analysis, we can know that simple addition of water can not be called wet method, but only to add part of the water, not to increase the material temperature, softening and part of the role of pre-cured material.
Due to the different properties of the material entering the barrel during the dry/wet condition, the wet method enters the barrel as a hot, soft material, and the dry method into the barrel is a hard, cold material. Therefore, the spindle system and the extrusion screw The configuration requirements are also different. In general, the dry machine equipped with a steam conditioning system can produce wet production, the efficiency will increase, but not as efficient as a dedicated wet machine model; wet machine models need to consider the impact of raw materials on the shafting during dry production. Some materials can be dry produced, but the efficiency will be reduced, but not for some materials. In other words, dry machines can be produced wet, while wet machines are not necessarily used dry. When choosing a bulking equipment, you can refer to the following principles:
First, according to the extruded material and purpose, it is determined from the structure whether to use a single screw extruder or a twin screw extruder, generally:
Single-screw extruder: Suitable for processing all kinds of raw materials and ordinary livestock and poultry compound feed.
Twin-screw extruder: The final product requires well-formed and beautiful appearance, uniform aging and uniform density adjustable feed (aquatic feed, pet food) and high value-added raw materials (starch, tissue protein). It should be noted that the above division is not absolute. For example, we propose to use twin-screws to produce aquafeeds. However, many companies currently use single-screws to produce aquafeeds. Many articles have introduced the difference between the two used in aquafeed production. In short, twin screw has the following advantages over single screw:
Produce high, up to 98% or higher.
The granules are formed well and the shape of the granules is uniform. The twin-screw die-out pressure is very stable, ensuring consistent pellet formation.
The twin screw's unique strong pumping capability ensures no back-jet or plugging. After stressing quality, the steam content in the material is relatively high, and the single screw is prone to overflow steam and back spray in the feed area, resulting in unsteady material flow, and the twin screw will not have a similar situation.
Can continuously and stably produce all kinds of small particles. In the production of 2mm and below diameter particles, the single-screw working conditions are unstable, the production rate will drop sharply, and the material type will also be worse.
Density control is more stable and reliable. The material is more fully and evenly melted in the twin-screw barrel, which can accurately control the production of floating materials, submerged materials and slow-sinking products.
Wide adaptability to the formula, more suitable for high-energy formula production. Twin-screws can produce high-energy formulations with 11-13% fat content (up to 17% in foreign materials), while single-screws generally do not exceed 6-8%.
Easy to operate, stable production process.
Because of the many advantages of twin-screws compared to single-screw production of aquafeeds, we recommend that twin-screw extruders be the preferred choice when producing such products. Of course, the investment and production cost of the twin screw must be much higher than that of the single screw, which should be considered according to the actual situation.
After determining the model, consider how the equipment works. For the twin-screw extruder, the wet method is used in principle, not only because of its high efficiency, but also the use of steam for the wet method and subsequent steaming of the drying equipment. Only with low output requirements (less than 500 kg/h) and without steam conditions, dry production can be used, but if the subsequent drying uses electric energy, the total energy consumption is also a factor to be carefully considered.
If you choose a single-screw extruder, from the current market situation, most of the single-screw extruder is used to make raw materials such as soybeans, corn and puffed whole-fat piglet production, whether it is the choice of dry or wet production methods To refer to the following conditions.
1. Puffed full price pig feed
The full-price compound feed is expanded (for the protection of vitamins and enzyme preparations, it is generally controlled within 105 degrees), broken, cooled, broken, and sieved to obtain finished products, which are now called “cooking materials†in the southern market. It started in Sichuan in 1996 and the market did not reflect well enough. It was re-emerged in the Guangxi region in 2000, represented by Yangxiang, and it was still a good market in Guangdong, Guangxi, Yunnan, Hunan, and other places. At present, it also has a tendency to expand to the north. This process originated from the expansion and granulation process of Zhengda System. From the cost factor, the granulation process was eliminated and the expanded scrap material was directly used as the final product. After this type of puffed piglet material, the general maturation degree is between 70 and 80% (there is also the practice of puffing part of the raw materials before puffing), which is higher than ordinary granulation, and the production cost is lower than that of expansion + granulation. Many manufacturers use full-price puffed pigs. This kind of full-price puffed milk pig feed must be produced by wet method. The surface of the dry product is easy to be compacted, has a large density and poor palatability.
2. Expanded soybeans, corn
Extruded soy flour should, in principle, be produced by wet methods as long as steam conditions exist. High wet production efficiency. Under the condition of the same power, the wet extruded pulverized soybean powder is more than double the dry process. For example, when the 90KW dry expanded pulverized soybean powder produces 800 to 1,000 kilograms, the wet method can produce up to 2500 kilograms. The EXT155S of the machine produced more than 2,800 kilograms of extruded soy flour at Wen's Group, which ranks first in the domestic market for efficiency and is one of the mainstream models on the market. The wet puffing control urease activity is more stable and can be accurately controlled between 0.02 and 0.2. The dry extruding soybean meal urease activity fluctuates greatly, and it is prone to uneven cooking. The moisture content of the wet extruded soybean powder can be accurately controlled at about 12%, while the moisture content of the dry product is only about 8%, and the production cost due to dry consumption is greatly increased. Extruded soy flour is used for its own use. When the amount is not high, a dry method is recommended, which is insensitive to the moisture content of the product. A dry machine is more appropriate. If soy flour is used for sale, we recommend the use of wet machines. First, the efficiency is much higher than that of the dry process. The production cost is significantly lower than that of the dry process. Second, the moisture content of the finished product is relatively easy to grasp. In some regions, the dry expanded soybean powder product is required. , you can stop production, the same can meet the requirements.
Although the efficiency of wet extruded puffed soybean meal is high, a large number of customers in Guangdong Province are currently favoring the dry puffed soybean meal, which may be due to the strong aroma of the dried product and its better attractantness. Therefore, many manufacturers use dry puffed soybean meal.
Because of the special properties of corn, extruded corn for feed can be produced using dry wet methods. Different from soy and other oils and fats, the quenching and tempering process is not as good as soy, because the quenching temperature is too high and the steam volume is too large to cause transportation problems, which leads to feed return and jamming. Therefore, corn requires less steam for conditioning. Significantly, the wet process can be increased by about 15% compared with the dry process. If the quality of the steam is not stable, the moisture of the material entering the machine will fluctuate, which will easily cause jamming and product quality fluctuations. Therefore, the wet-expanded corn is more demanding for operators, and it is necessary to pay attention to changes in steam and final products at any time and make corresponding adjustments. The main index of extruded corn is the degree of gelatinization and the bulk density (a separate article), and the dry or wet bulking should be determined according to the use of the product. Extruded corn flour, if used for sale, is recommended for dry type. Due to dry puffed corn, the puffing degree can be adjusted to a wide range. It can reach high puffing degree (finished product weight ≤200g/L), and can satisfy different users. Requirements, less investment, quicker results. If you use (process feed), you can consider the wet method, the yield is slightly higher than the dry method, starch gelatinization degree can reach more than 85%, although the expansion degree is not as high as the dry method, but the effect is very good after the mixture is made. It should be pointed out that the degree of puffing of corn required by special fur animals is higher than that required by suckling pigs, and most of the bulk density is about 0.3. Therefore, the requirement for puffed corn in northern areas is higher than that in the south. At present, in theory, the bulk density of 0.4 to 0.5 can be used for sucker feed, but users tend to use the requirement of fox feed to choose expanded corn. Therefore, if the expanded corn flour is used for special animal feed (eg, fox, fox, quail, etc.), the dry method should be used because of the high requirements for bulking and maturation, and dry and wet methods can be used if it is used for the preparation of baby pigs. As mentioned earlier, some wet machines cannot be used for dry processes, such as the production of expanded corn, and the wet machine expansion products generally have an aging degree of about 85%, a bulk density of 0.4-0.5, and a temperature of 140-150°C. Increased degree of expansion and puffing, such as a bulk density of 0.2, and a temperature of 160-170°C, may need to be achieved by turning off the steam tempered dry process. Because the difference in the material properties of the engine causes a sudden increase in torque and thrust (compared to the wet method), whether the spindle or bearing housing structure can withstand or not, and whether the bullet head can withstand corrosion at high temperatures requires practice and time to verify. Many wet machines on the market currently do not have the ability to dry produce high-strength corn flour.
There are many users to buy expanded equipment is to process corn, soybean two materials, in addition to the above, but also consider that if the expected production of the two products are not very high, roughly the same, you should use a dry machine. Because the output of wet machine-expanded corn and soybeans is very different, if there is little time for soybean puffing in use, it is mainly used for corn puffing. In this way, the steam system and the configuration of conditioners are not obvious, that is, the same production targets. , The investment is much higher than that of the dry unit.
3. Extrusion of other materials
Expanded feather powder can only be dried, and the raw material is as dry as possible.
Extruded corn urea can only be dried. Steam will melt the urea in the conditioner, resulting in agglomeration and sticking.
Extrusion rice bran pressing oil should use dry method, fresh treatment can be used wet method.
It is advisable to use the wet method for the detoxification of cottonseed meal, vegetable dish, and ramie.
Expanded blood meal, fish meal dry wet method can be.
The above describes some basic principles for selecting the working mode of single-screw bulking equipment. The steam conditions and investment quotas are also important factors that restrict the selection of models. Those who have steam conditions and have sufficient funds can choose large-size wet-type models; otherwise, they choose Small model dry machine.
staff and provides patients with a high-quality hospital experience. At the same time, the company maintains long-term close cooperation with universities and large medical groups, and enters the medical engineering industry such as
medical intelligent sharing and accompanying systems, medical logistics storage systems, and operating room purification systems.
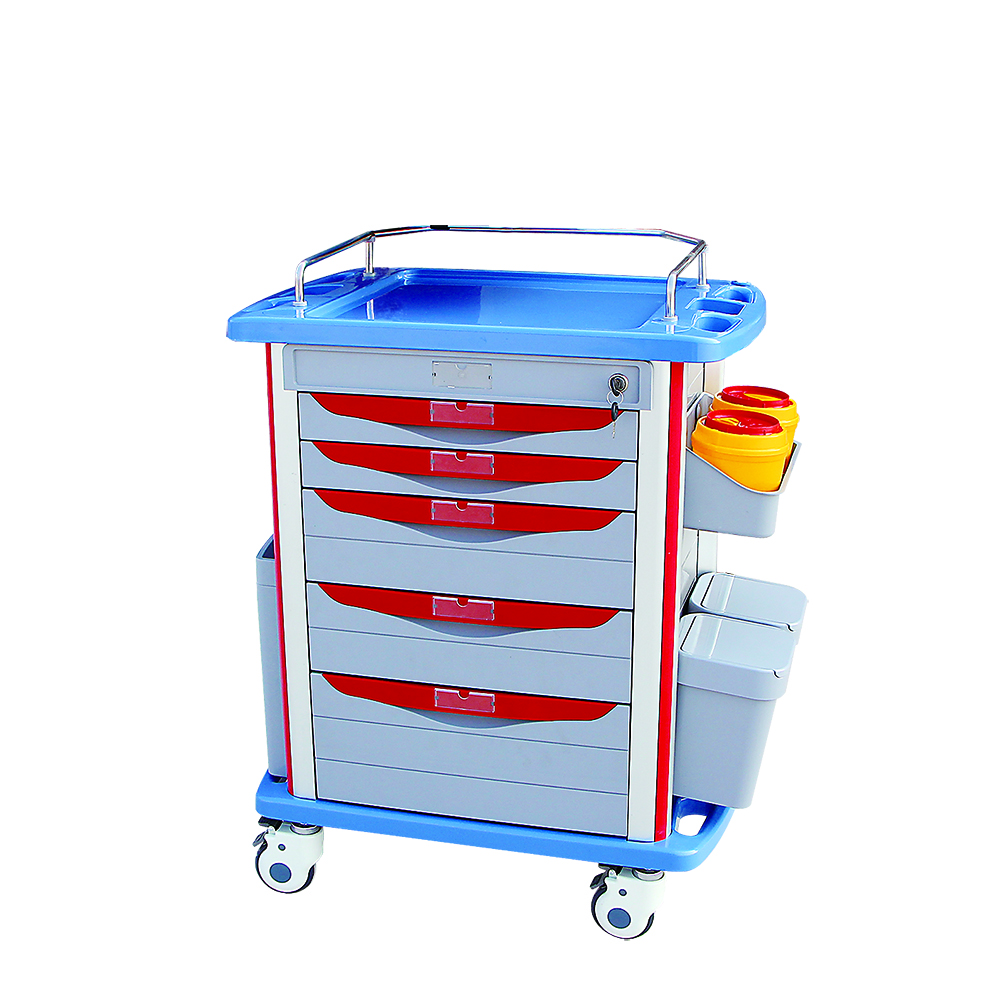
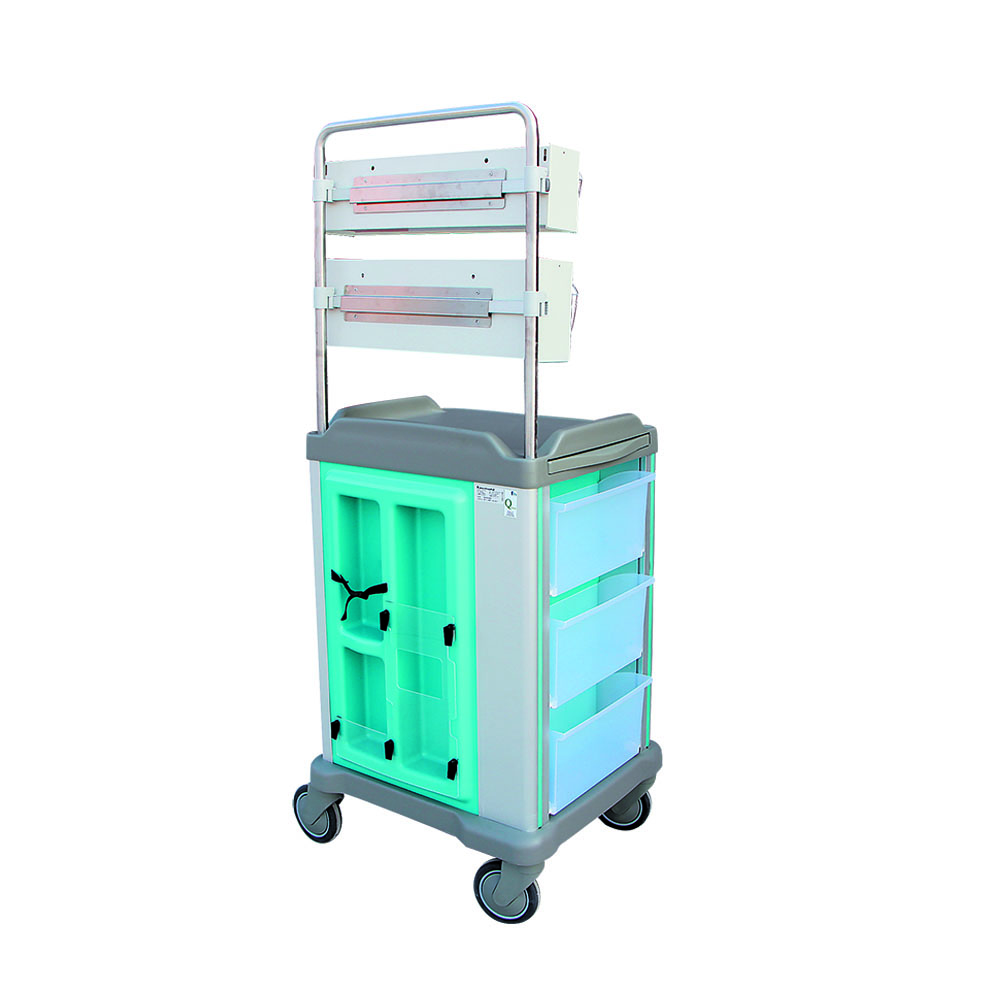
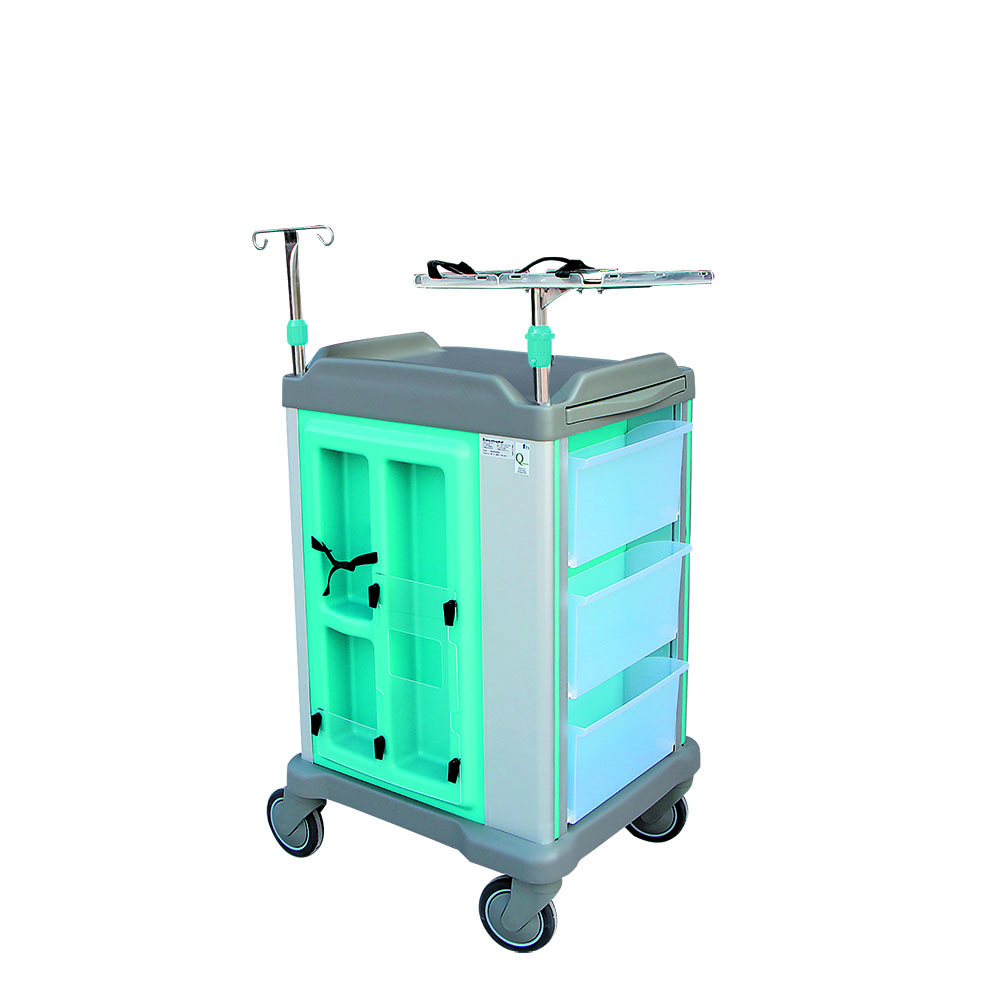
Emergency Trolley,Stainless Stell Trolley,Mobile Emergency Trolley Carrying Drugs,Emergency Trolley With Drawers And Wheels
Shanghai Rocatti Biotechnology Co.,Ltd , https://www.ljdmedical.com